AUTOMATIC LINES WITH GAS LOAD
DESCRIPTION
All double-glazing production lines adopt a modular concept and can, therefore, be adapted to the needs of the individual customer.
Made up of 3 m modules, the glass is transported via a system of anti-cut rollers with frictional components to increase the safety of the operator.
The washing machine body is in powder-coated stainless steel and is 2.6 m long. All components in contact with water are corrosion resistant and equipped with 6 x 160 mm diameter brushes with steel shafts and aluminum supports.
The water management group is made up of three washing areas with tanks, pumps, filters and internal parts in stainless steel.
Thanks to the shape of the tanks, water consumption has been reduced to a bare minimum reusing wastewater from one sector to another. The thermostat-controlled heating system is standard over the entire range.
A fan for drying has been installed in an insulated box to reduce noise, with a damper to manage the air flow allowing for greater energy saving during processing stops. The working speed is adjustable and controlled exclusively by an electronic system that maintains the torque constant even with different weights.
The output module is equipped with a new continuous LED light system to allow better control of the washing quality.
The motorised assembly is made up of double anti-cut rubber rollers mounted on friction systems. The transport is managed by an inverter which allows the processing speed to be increased during the movement of the glass, reducing waiting time to a minimum. Thanks to the LED light system it is possible to identify any imperfections on the glass.
A laser sensor guarantees high positioning precision of the profile. The pneumatic movement pistons are controlled by oil-filled clearance adjusters, and managed by sensors that read the thickness of the glass to allow the operator to position the groove without any adjustment while working on different glass thicknesses.
The measurement module allows you to automatically detect all the quantities to calculate the volume of gas needed.
The 3.15 m long panel press is equipped with anti-cut friction rollers. The work surface moves via a sliding system mounted on recirculating ball bearings, controlled by spiral clamps connected to each other by a high-precision belt, maintaining perfect parallelism with both small and large glass panes.
The pressing force is controlled by an electronic system which guarantees the correct result through the micro torque adjustment of the Brushless motor which controls the movement. The press automatically regulates the pressing force via sensors that read the dimensions of the glass, and through the new self-management software.
The EASY TOUCH control panel with a simple touch screen allows the operator to control the working process, adjust the machine parameters and check the individual operation of each component.
The fixed exit is made up of a 3 m module. The glass is transported via a system of anti-cut rollers mounted on frictional components to increase operator safety.
Self-learning system of the measurements of the glass being processed for automatic gas loading, with ad hoc adjustments on the control panel.
The machine has been designed to be connected to other work modules.
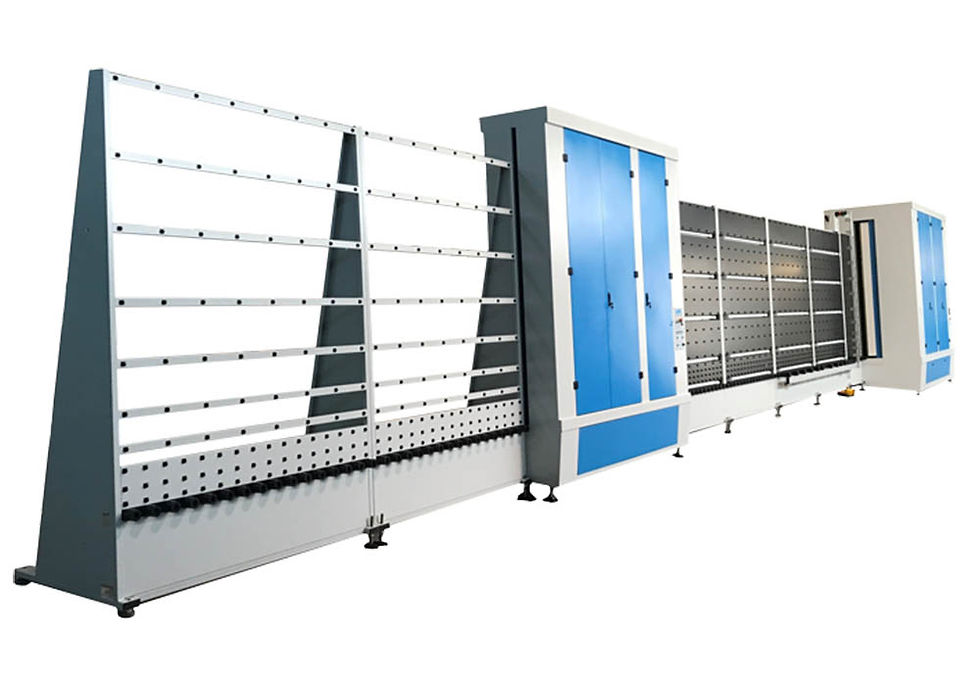
ALWAYS CONNECTED
All automatic lines can be connected to our monitoring centre simply by connecting the line to the internet with the following advantages:
-
Possibility of remote troubleshooting;
-
Reduction of machine downtime;
-
Instant control of the aging of electronic components;
-
Possibility of excluding sensors to be able to continue production while waiting for a spare part (provided it doesn’t compromise the operator's safety).
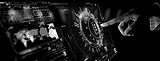
TECHNICAL SPECIFICATIONS
Power supply
400 Vac Three-phase + Neutral 50 Hz
Total consumption
26 Kw 400 Vac 50 Hz
Washing brushes
6 standard 160 mm brushes
(optional LOW-E)
Washing zone
3 separate zones with ECO WATER system
Washable glass measurements
Min 350 x 250h mm approx.
Max 2900 x 2000h
(Max 3000 x 2000h with 4 m modules)
Washable thickness
From 3 to 14 mm
(optional up to 20 mm)
Panel press thickness
80 mm approx.
Work direction
From left to right
(optional from right to left)
Working speed
From 3 to 8 m/minute
Work surface
600 mm approx.
Height
3000 mm approx.
Length
20 mt approx.
Width
2000 mm approx.
Weight
4400 Kg approx.
We recommend water supplied to the washing machine has the following characteristics:
Conductivity = less than 10 uS (microsiemens)
Hardness total = less than 5° F (French degrees)
Salt content = less than 5 mg/L
Chloride = less than 5 mg/L
Iron = less than 0,05 ppm
Torbidity = less than 0,5 ft
NB: The results of the window washing may be compromised if the water values are higher than the above recommended amounts. Upon request we can provide equipment for cleaning the water.
FEATURES

WATER RECOVERY
Water is a precious resource - the washing system is designed for a double reuse of water, avoiding unnecessary waste while maintaining optimal quality at the end of the process.

LONG-LASTING
Attention to durability over time is synonymous with quality - All parts of the machine in contact with water are made of powder-coated stainless steel, brush supports and tows in aluminium, stainless steel pipes, and brass spray nozzles.

ENERGY SAVING
Consumption is significantly reduced during processing thanks to a system which reduces motor consumption while maintaining the air flow active.

SAFE TRANSPORT
The safety of the operator is fundamental, but the glass has to be moved for processing. The system adopted allows the glass to be blocked at any time with the rollers moving. All this thanks to an innovative type of transportation.
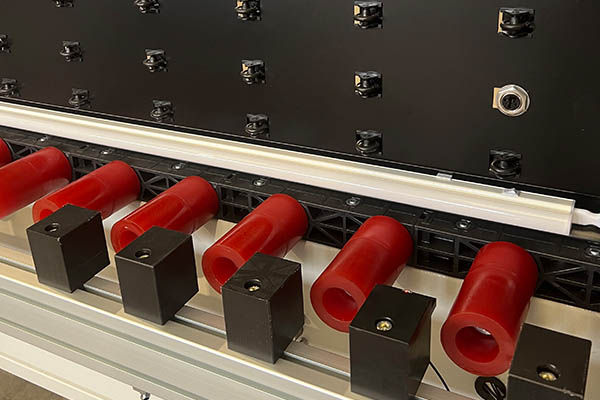
LASER PRECISON
The manual component of the line is in the assembly module where the operator places the profile. It is therefore essential to give all the references to the operator quickly and precisely. Thanks to the laser reading system it is possible to have high positioning precision and therefore reduce processing times.

SIMPLE AND RELIABLE
The assembly guarantees perfect positioning of the profile bar through this new system using a mix of pneumatics and hydraulics.

ELECTRONIC PRESS
The choice adopted to use is a type of press controlled by an electronic system and transmitted uniformly to the entire work surface.
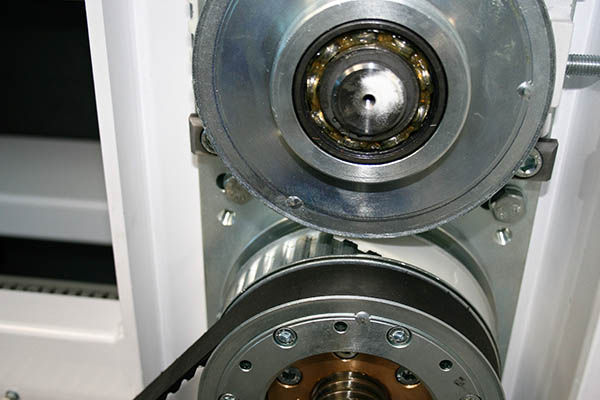
STRENGTH CONTROL
Unlike classic pneumatic pressers this system allows micrometric adjustment of the press, by modifying the electronic parameters of the Brushless motor. The final result is clearly superior, guaranteeing excellent adhesion to the first butyl barrier and avoiding crushing the profile between the two panes of glass.
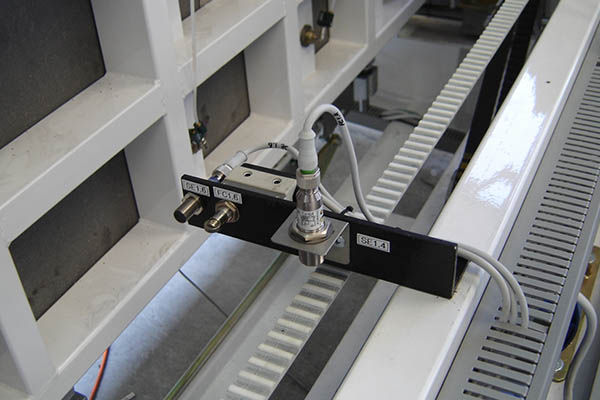
SELF-LEARNING MEASUREMENTS
The machine can autonomously learn the dimensions of the glass to adjust the pressing force. The operator's task is to set the initial torque and the time, then everything else is managed by the new control software which allows the pressing to be kept constant while varying the dimensions of the glass.

ROBUST BUT FAST
The press body is made up of a network of steel tubes designed to avoid any twisting of the machine during the pressing phase. The movement is managed by a zero-backlash toothed belt which distributes the force from a four-point BRUSHLESS motor anchored to the moving table. The result guarantees perfect parallelism in the pressing phase.

RELIABLE GLASS GRIP
The glass is kept firmly anchored to the moving surface thanks to the vacuum generated by several independent rubber suction cups. Thanks to this decentralised vacuum system, the release of the glass is avoided in the event of a fault.

TOUCH SCREEN COMMANDS
The EASY TOUCH control panel is simple and intuitive and allows the operator to manage the entire line and control all the parameters of the machine. Thanks to this system the machine can be connected to our headquarters for maintenance and any machine downtime resolutions.


DOUBLE OR TRIPLE GLASS
Thanks to a simple touch button it is possible to define the type of production, double or triple glass.

PLUG IN COMMUNICATION
All the line connections are modular with special plugs and sockets dedicated to strength commands, and the control of digital communication signals. The line has been designed to work with other modules such as the sealing robot, warehouse transfer or tilting table.

OPENING FOR MAINTENANCE
Thanks to the movement system adopted, it is possible to open the machine up to 350 mm allowing the possibility of carrying out maintenance without having to dismantle any components.

GAS OPTIMIZATION
Thanks to our gas management system, unnecessary consumption is avoided by guaranteeing uniform diffusion throughout the glass being processed.

GAS CONTROL
The control of the gas on multiple areas guarantees perfect diffusion without creating air pockets that could jeopardize perfect filling.

ADDITIONAL GAS REGULATIONS
The machine can independently calculate the gas loading volume. The panel shows all the parameters necessary for filling the gas, also allowing for micro-adjustment by the operator.
OPTIONALS
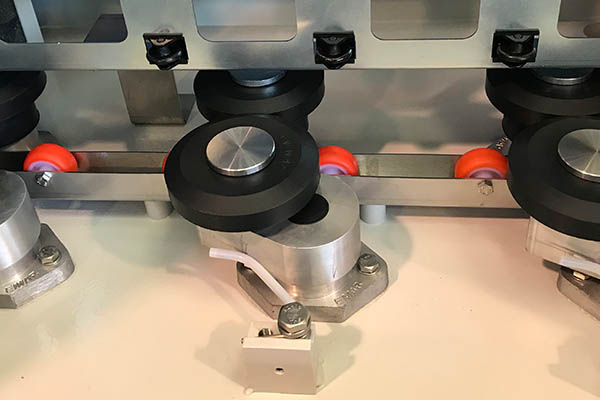
THICKNESSES UP TO 20 mm
Thanks to the self-aligning opening system it is possible to process glass thicknesses from 3 to 20 mm completely automatically.

TILTING EXIT
3 m folding output module operated by a jack controlled by an electronic inverter. The module can be used both as a fixed storage and a sealing table.

LOW-E BRUSHES
These type of brushes use special bristles that allow you to work with more delicate glass. They are complete components with a stainless steel shaft.