SEMI-AUTOMATIC LINES / STANDARD
DESCRIPTION
All double-glazing production lines adopt a modular concept which can be adapted to the needs of the individual customer.
Made up of 3 m modules the glass is transported via a system of anti-cut rollers, with frictioned components to increase operator safety.
The washing machine body, in powder-coated stainless steel, is 2.6 meters long.
All components in contact with water are corrosion resistant.
The machine is equipped with 6 brushes with a diameter of 160 mm with steel shafts and aluminum supports.
The water management group is made up of three washing areas with tanks, pumps, filters and internal parts in stainless steel.
Thanks to the shape of the tanks water consumption has been reduced to a minimum, reusing wastewater from one sector to another.
The thermostat-controlled heating system is standard over the entire range.
Drying is served by a fan mounted in an insulated box to reduce noise with a damper to manage the air flow and therefore allow greater energy saving during processing stops.
The working speed is adjustable and controlled exclusively by an electronic system that maintains the torque constant even with different weights.
The output module is equipped with a new system of continuous LED lights to allow better control of the washing quality. The transport of the glass takes place via a system of anti-cut rollers, mounted on frictioned components to increase operator safety.
Thanks to the LED light system it is possible to identify any imperfections on the glass.
High profile positioning precision is guaranteed thanks to a laser sensor. The pneumatic movement pistons are controlled by oil-filled clearance adjusters managed by sensors to read the thickness of the glass, so that the operator can position the channel without any adjustment while working on glass of different thicknesses.
The 1 m roller press is equipped with anti-cut friction supports and moves via pneumatic pistons made of material treated with bushings.
The machine can be adjusted by the operator to vary the pressing thrust.
The fixed exit is made up of a 3 m module with the glass transported via a system of anti-cut rollers mounted on frictioned components to increase operator safety.
The machine, as standard, has been set up for connection to other work modules.

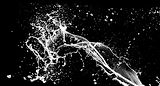
TECHNICAL SPECIFICATIONS
Power supply
400 Vac Three-phase + Neutral 50 Hz
Total consumption
22 Kw 400 Vac 50 Hz
Fan motor
4 Kw 400 Vac Three-phase 50 Hz
Hot water resistance
4,5 Kw 400 Vac 50 Hz
Washing brushes
6 standard 160 mm brushes
(optional LOW-E)
Washing zone
3 separate zones with ECO WATER system
Washable glass measurements
Min 350 x 250h mm approx.
Max 2900 x 2500h
Washable thickness
From 3 to 14 mm
(optional up to 20 mm)
Panel press thickness
50 mm approx.
Work direction
From left to right
(optional from right to left)
Working speed
From 3 to 8 m/minute
Work surface
600 mm approx.
Height
3400 mm approx.
Length
16 mt approx.
Width
1500 mm approx.
Weight
4000 Kg approx.
We recommend water supplied to the washing machine has the following characteristics:
Conductivity = less than 10 uS (microsiemens)
Hardness total = less than 5° F (French degrees)
Salt content = less than 5 mg/L
Chloride = less than 5 mg/L
Iron = less than 0,05 ppm
Torbidity = less than 0,5 ft
NB: The results of the window washing may be compromised if the water values are higher than the above recommended amounts. Upon request we can provide equipment for cleaning the water.
FEATURES

WATER RECOVERY
Water is a precious resource - The washing system is designed for a double reuse of water, avoiding unnecessary waste while maintaining optimal quality at the end of the process.

LONG-LASTING
Attention to durability over time is synonymous with quality - All parts of the machine in contact with water are made of powder-coated stainless steel, brush supports and tows in aluminium, pipes in stainless steel, and brass spray nozzles.

ENERGY SAVING
Consumption is significantly reduced during processing thanks to a system which reduces motor consumption while maintaining the air flow active.

SAFE TRANSPORTATION
The safety of the operator is fundamental, but the glass must be moved for processing. The system adopted allows the glass to be blocked at any time with the rollers moving thanks to an innovative type of transportation.

EASY MAINTENANCE
Thanks to the type of construction, maintenance and cleaning are convenient, easy and quick.

NOISE REDUCTION
A fan for drying has been installed in an insulated box to reduce noise with a damper to manage the air flow allowing for greater energy saving during processing stops. The cleanness of the air is guaranteed by a removable filter.

DOUBLE OR TRIPLE GLASS
Thanks to a simple pedal it is possible to define the type of production (double or triple glass).
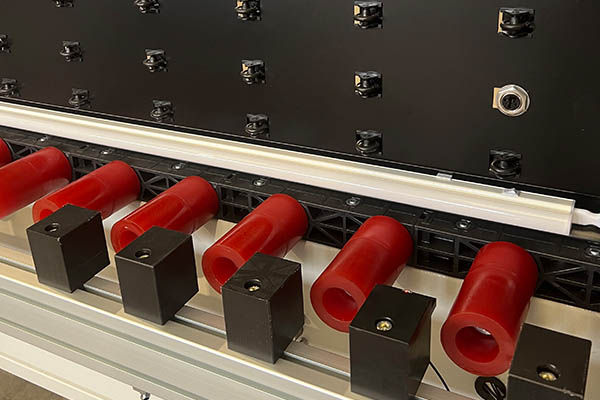
LASER PRECISION
The manual component of the line is in the assembly module where the operator places the profile. It is therefore essential to give all the references to the operator quickly and precisely. Thanks to the laser reading system it is possible to have high positioning precision and therefore reduce processing times.

SIMPLE AND RELIABLE
The assembly guarantees perfect positioning of the profile bar through this new system created from a mix of pneumatics and hydraulics.
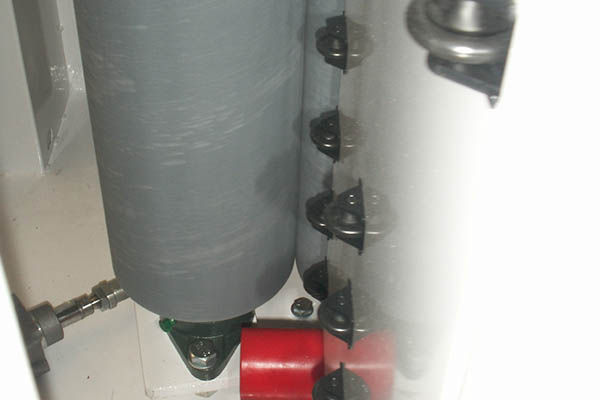
VULKOLLAN® ROLLER
Vulkollan® is a polyurethane renowned for its exceptional resistance to dynamic stress and abrasion, laceration and cuts, this material guarantees long life over time.

CONTROLS AND ADJUSTMENTS
All controls are situated in the front part of the press and are simple and intuitive, allowing the operator to dynamically and precisely adjust all pressing parameters.
OPTIONALS
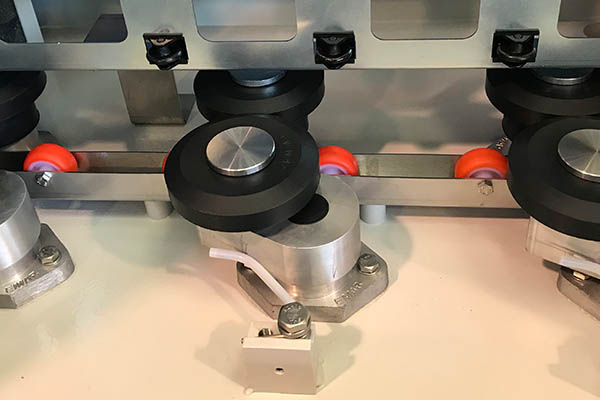
THICKNESSES UP TO 20 mm
Thanks to the self-aligning opening system it is possible to automatically process glass thicknesses from 3 to 20 mm.

TILTING EXIT
3 m folding output module operated by a jack controlled by an electronic inverter. The module can be used both as a fixed warehouse and a sealing table.

LOW-E BRUSHES
These type of brushes have special bristles that allow you to work with more delicate glass. They are complete components with a stainless-steel shaft.